BBB MAGAZINE
CREDIT
-
- ライター
- 執筆
NANDY小菅
-
- 撮影
NANDY小菅
-
- バイク
GSX1300BK B-KING

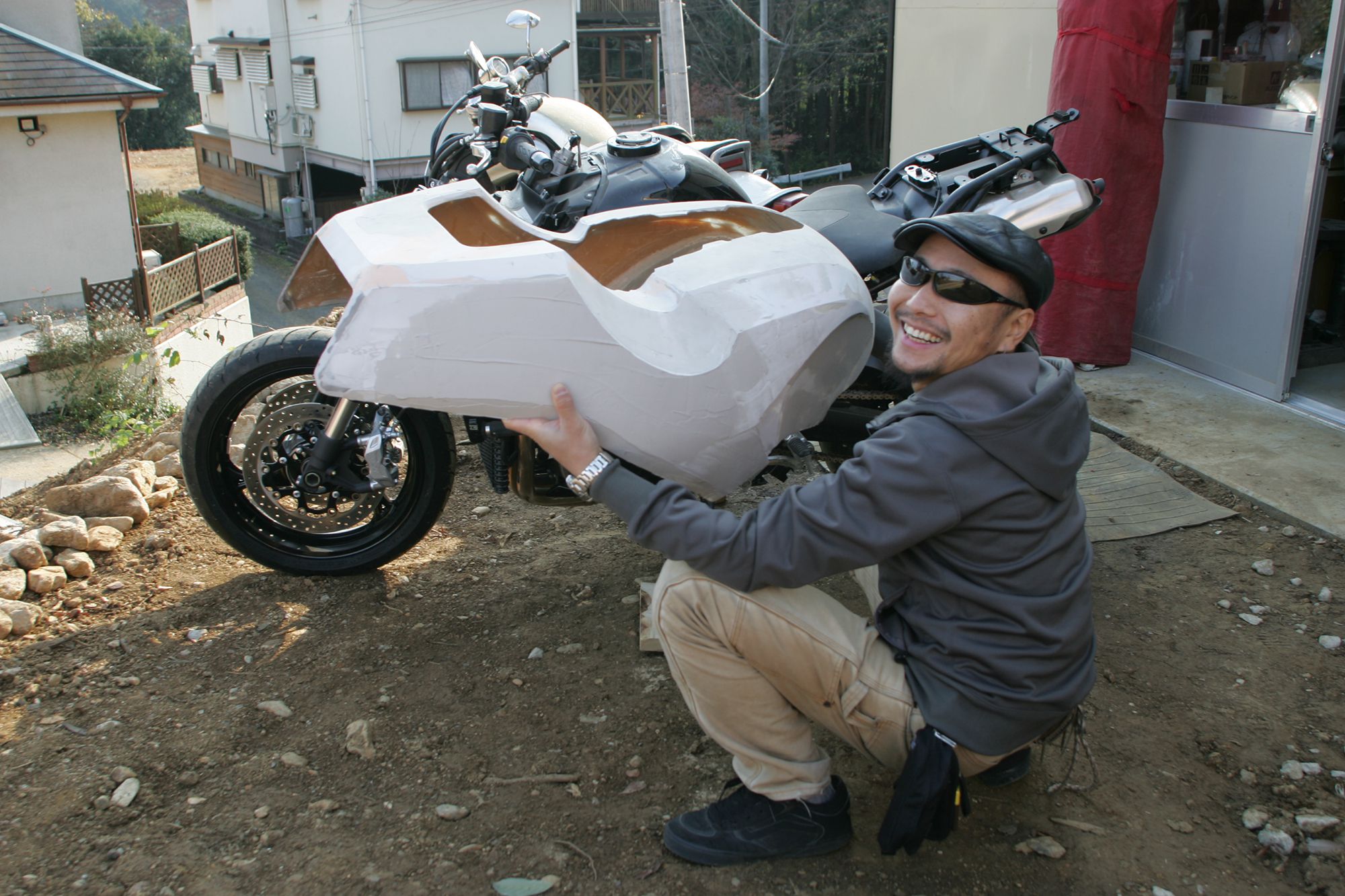
ライトケースの原型に関してはVol.11の段階から更にパテを盛って、表面にエッジを立てたりといった造形が続いている状態です。この状態まで出来たこともあり、ようやくライトケースの製作に着手していたわけですが・・・
ちょっとクリアランスが足りない気がしてきた
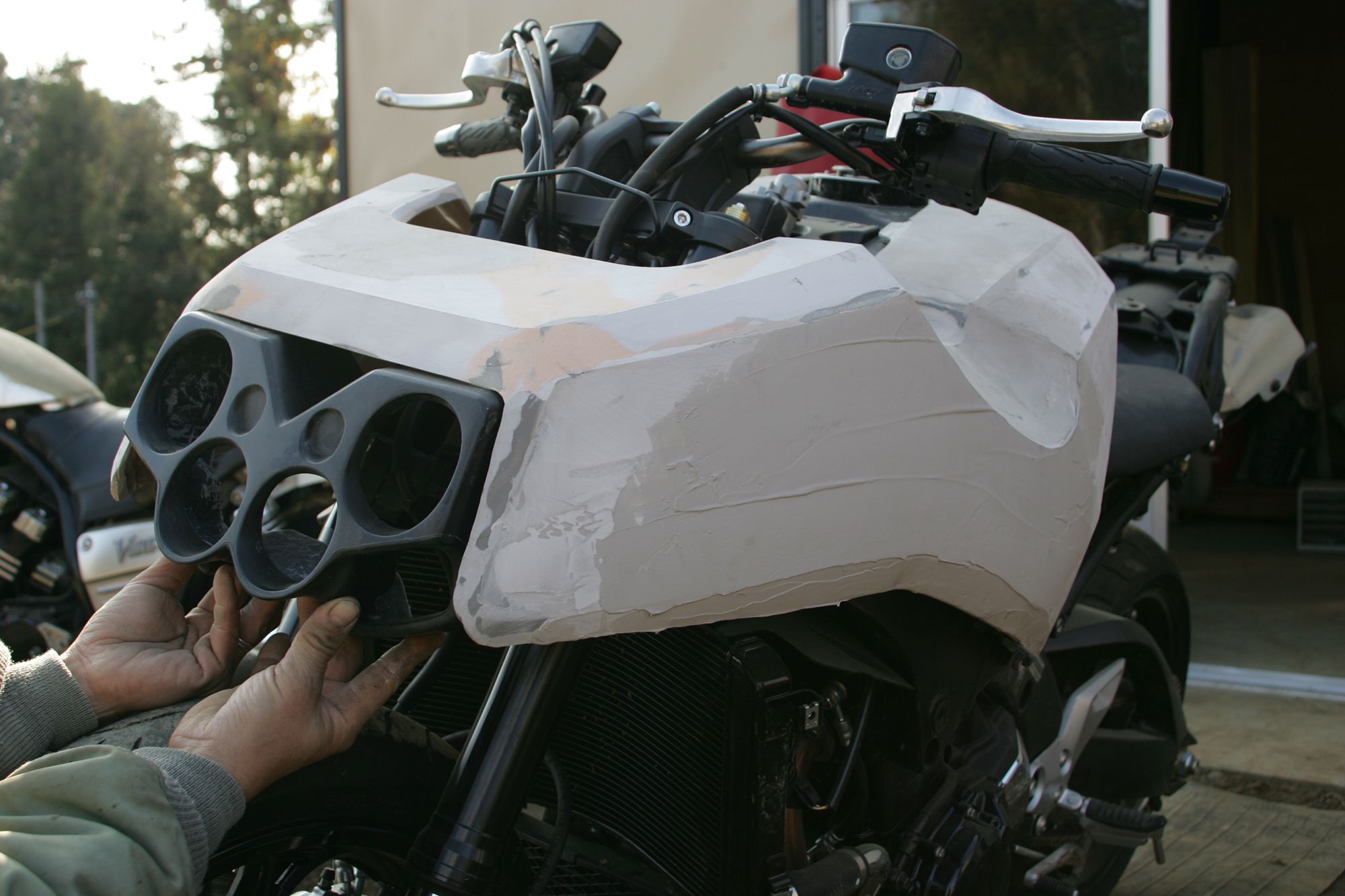
フロントタイヤとライトケースの隙間がこれではチト少ないかなーと。ブレーキングしたときにフォークが縮んだら、当たっちゃうかなーと思うわけですよ。
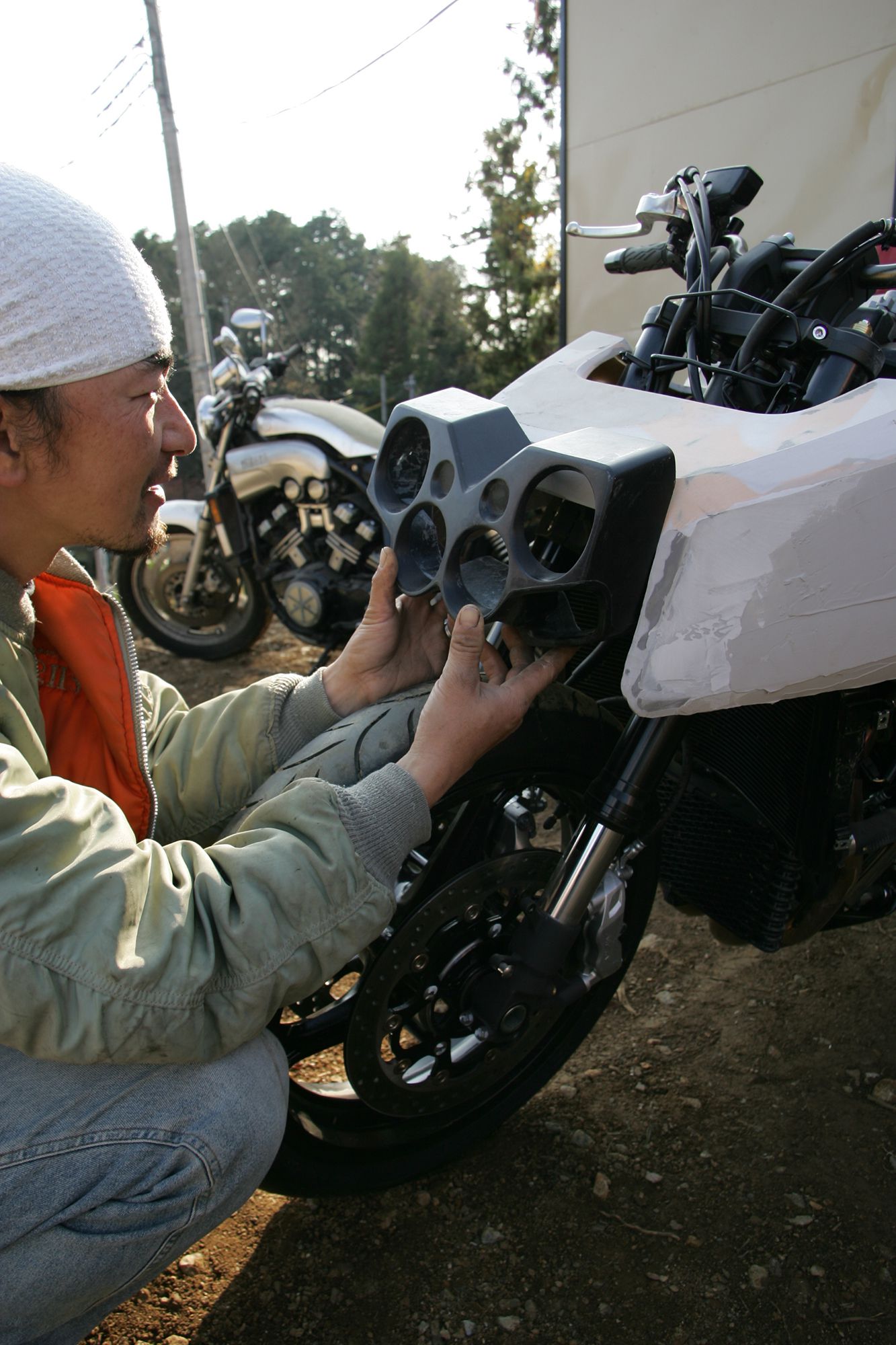
フォークの沈み込みを考えたらこれぐらいの余裕は欲しいところ。つまりライトケースを写真のような位置まで上げてマウントしなければならないのだが、正直アッパーカウルのサイド部分のデザインは崩したくないという葛藤が・・・。
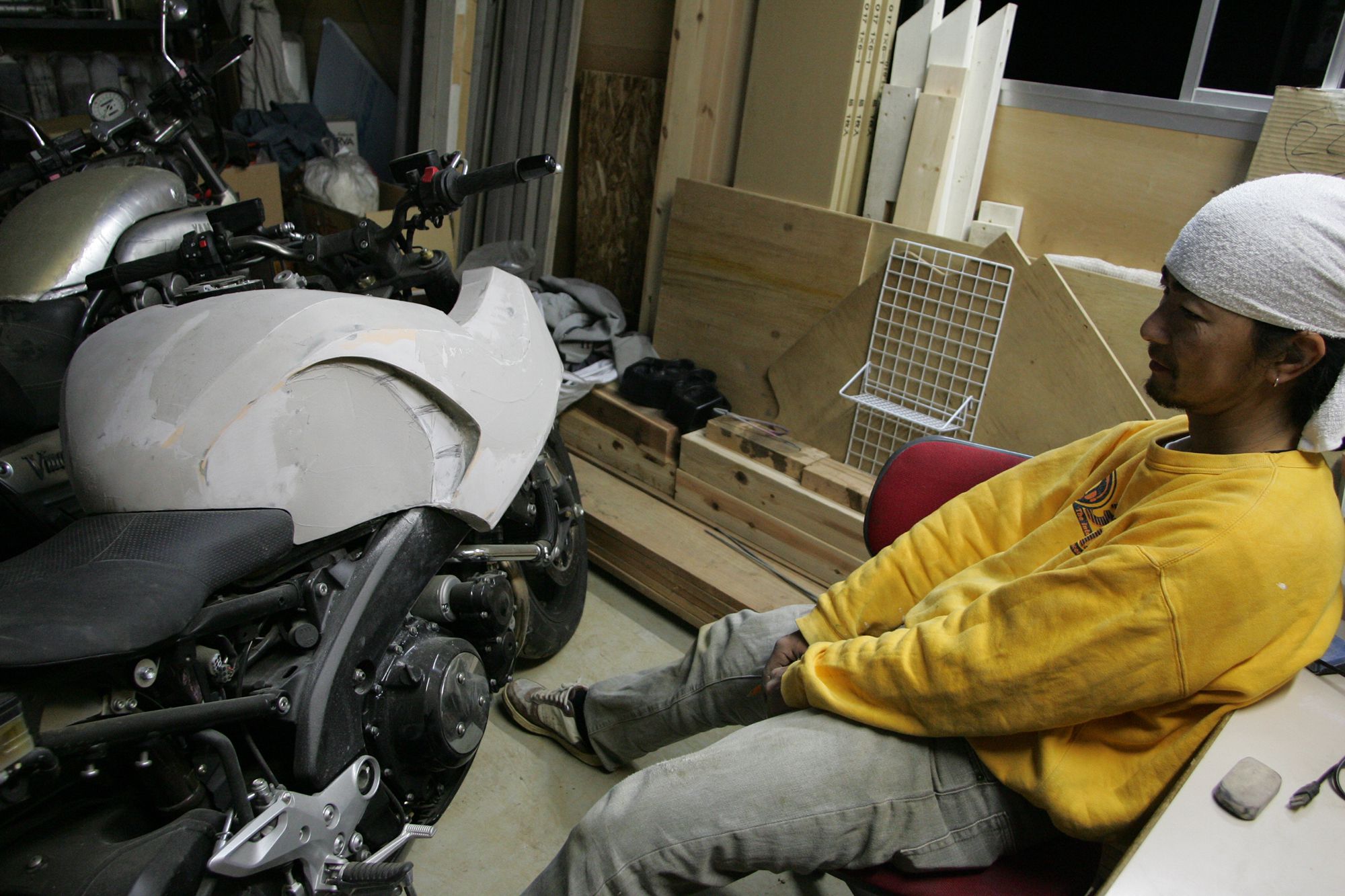
サイドダクトに入れるスリットデザインも想定しつつ、どうしたものかと考えるファニーズ川口さん。
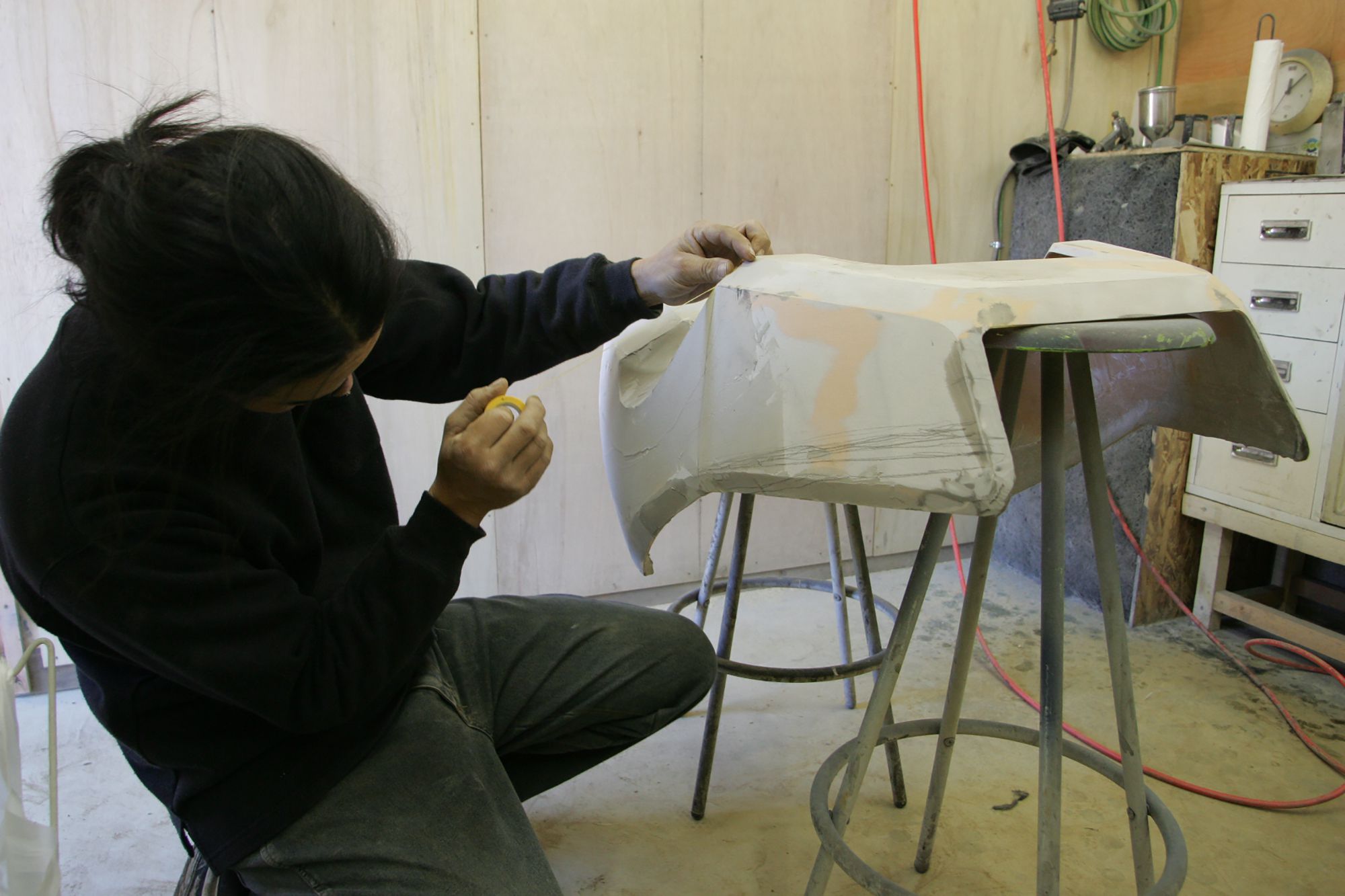
鉛筆で描いてみたラインでカウルを切って上面も作り直す案も出たが、アッパーカウルを前後で2つに切って、角度を変えてもう一度付け直す方向に・・・?
やっぱり切るしかない! 決断!!
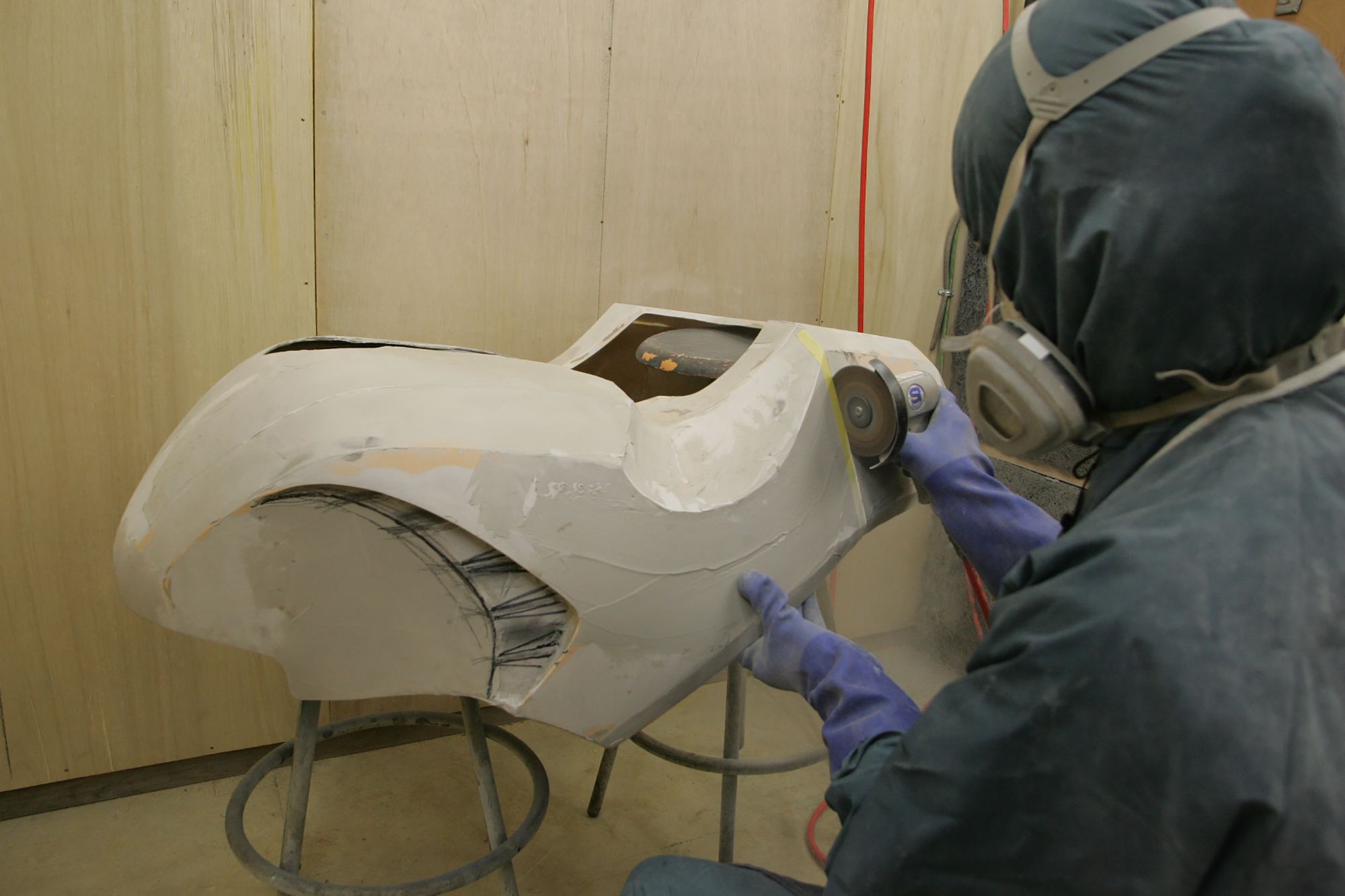
エッジ部分などに出来るだけ被害が少ないラインを考慮して、サンダーで切ります。
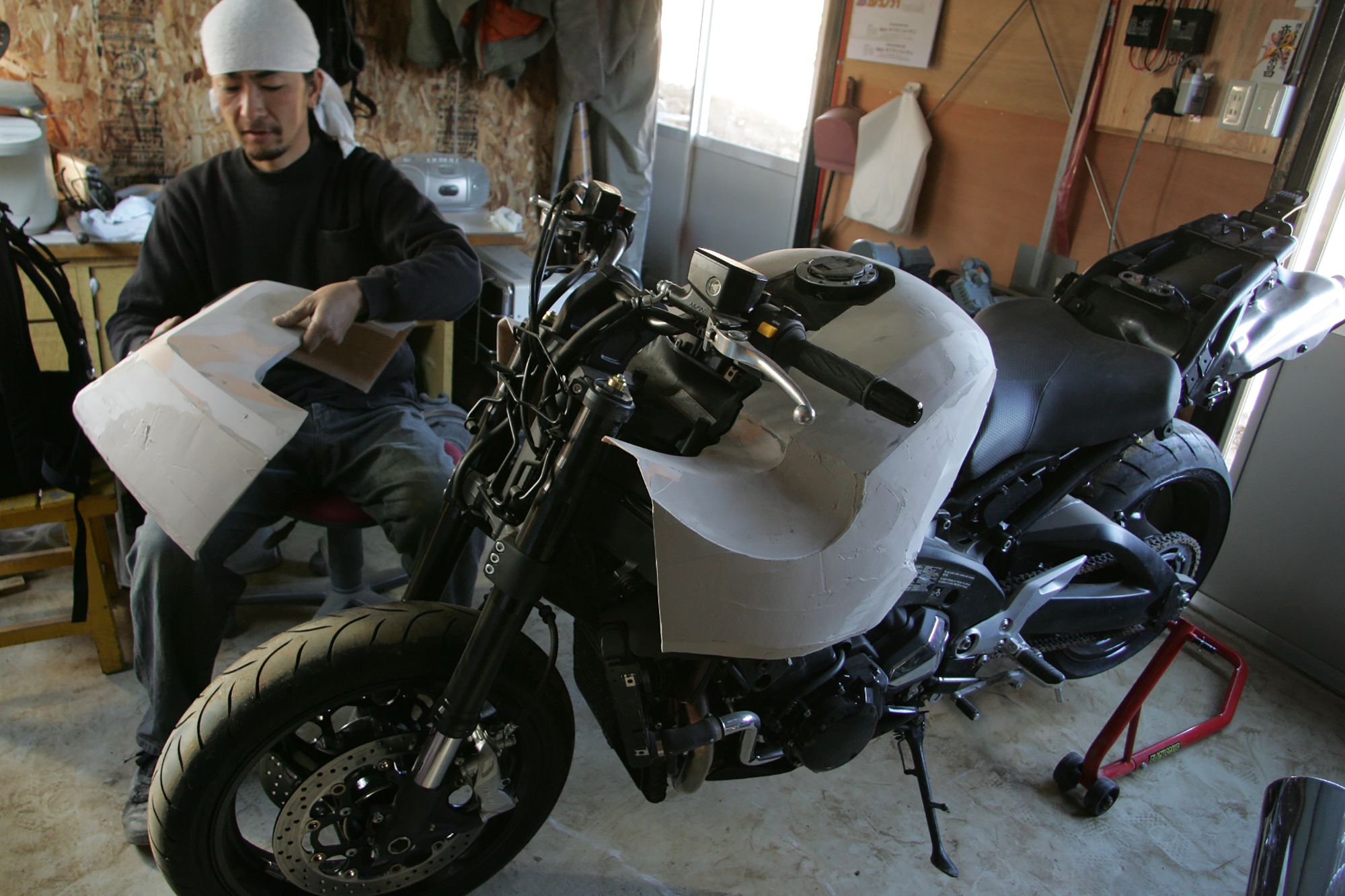
アッパーカウルを2つに分割した状態で、もう一度「デザイン的なライン」と「実用的な形状」を考え直すことにしました。
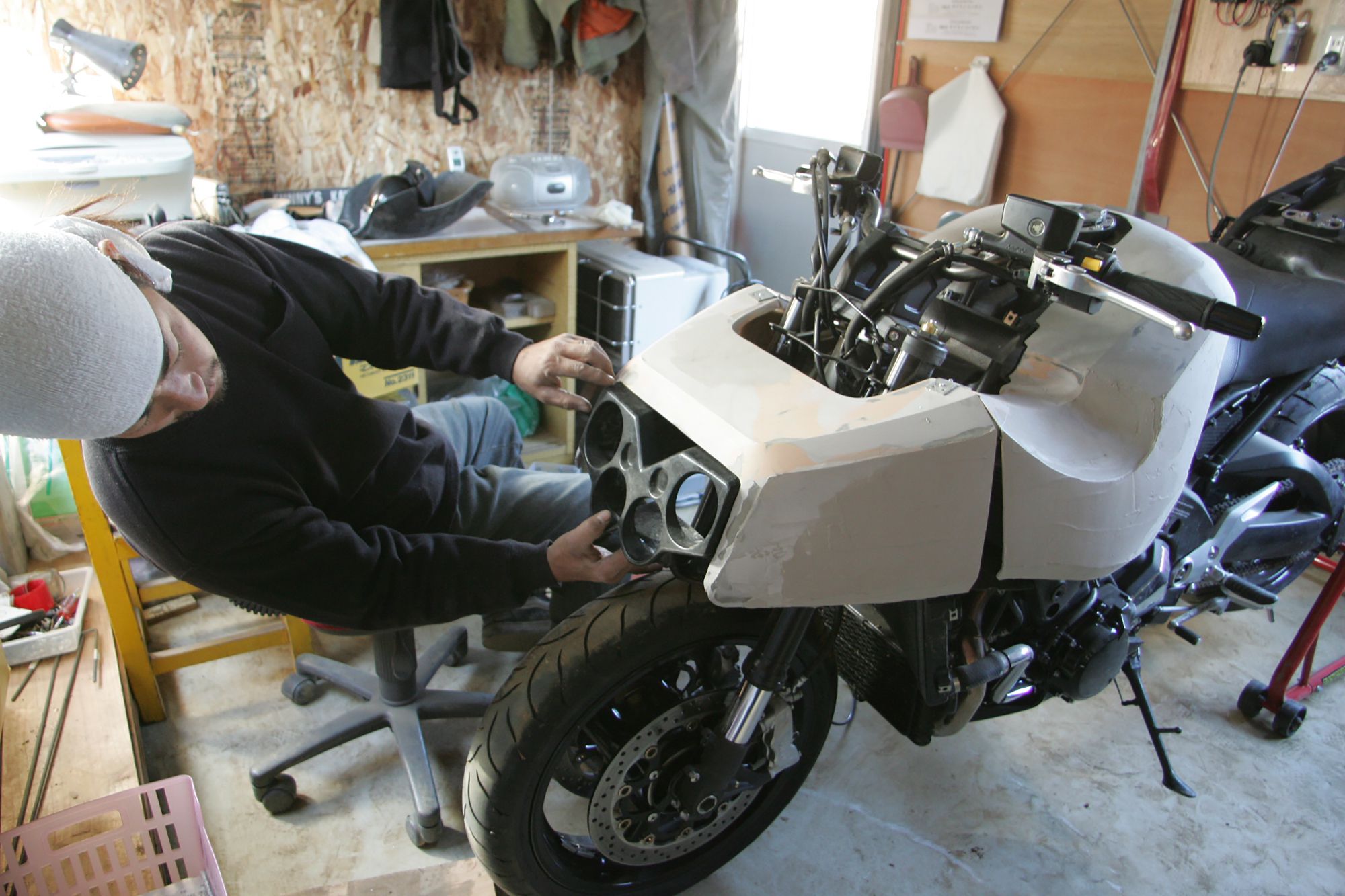
アッパーカウルをアルミのステーとリベットで仮止め。ホンのちょっとの角度の違いでライトケースも有効範囲内に収まりました。
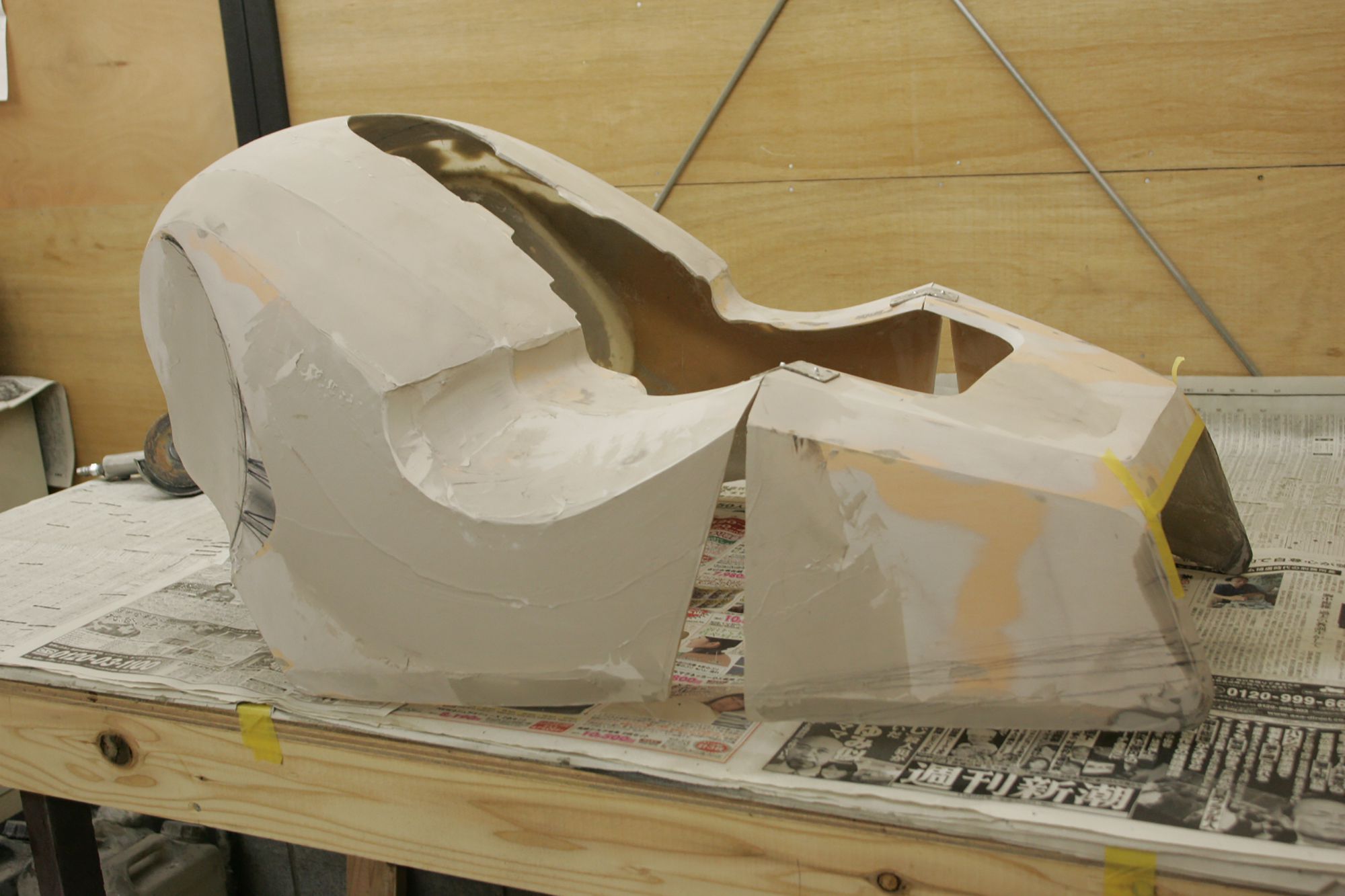
さて、ここからはこのカウルを繋げていく作業になります。カスタム好きな人にはFRP修正作業のご参考にしていただければと思います。
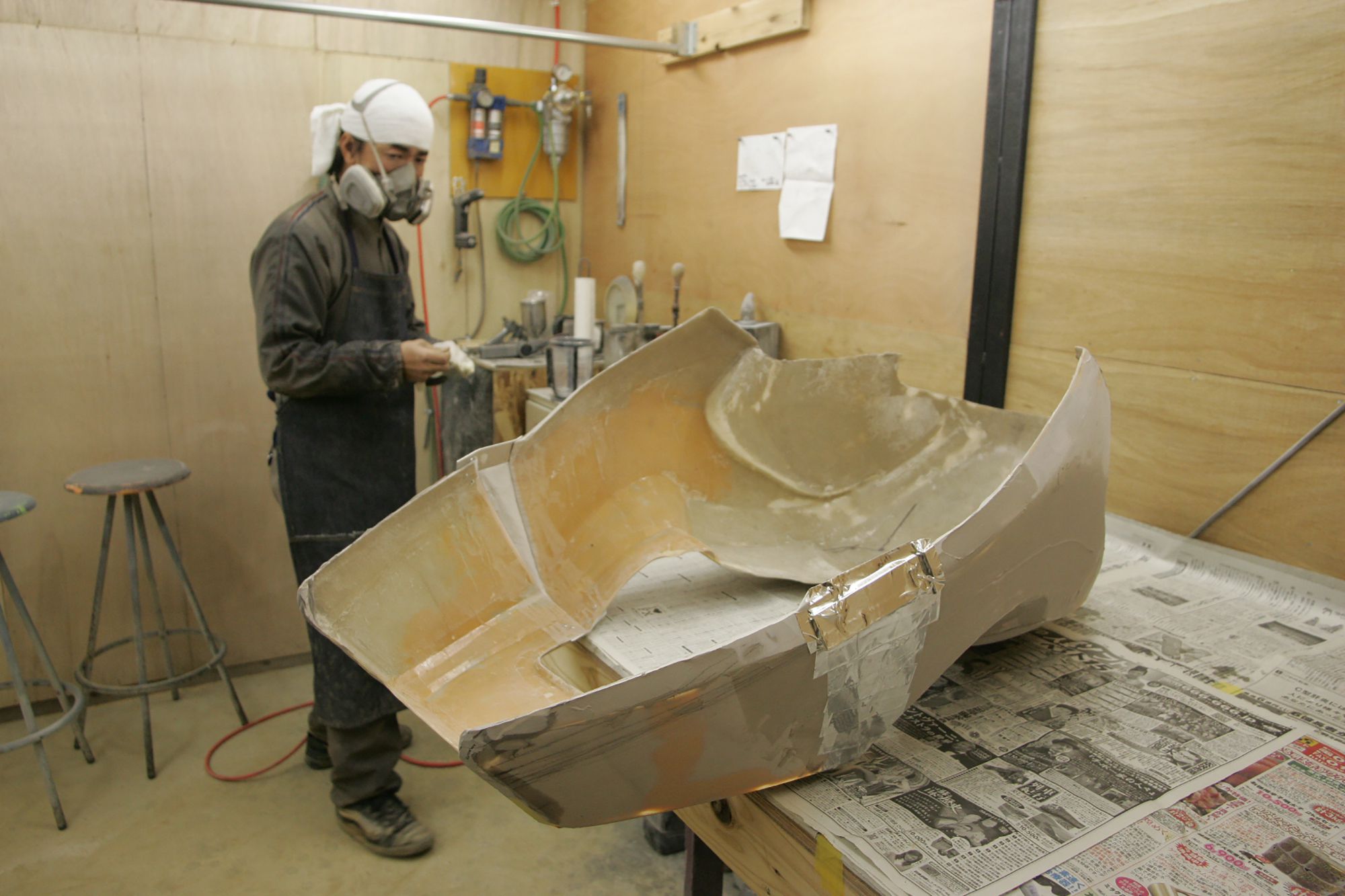
下側にもアルミのステーをリベット止めして、アルミテープを貼ります。ステーやアルミテープを貼るのは全て外側からで、FRPを貼るのは内側からになります。
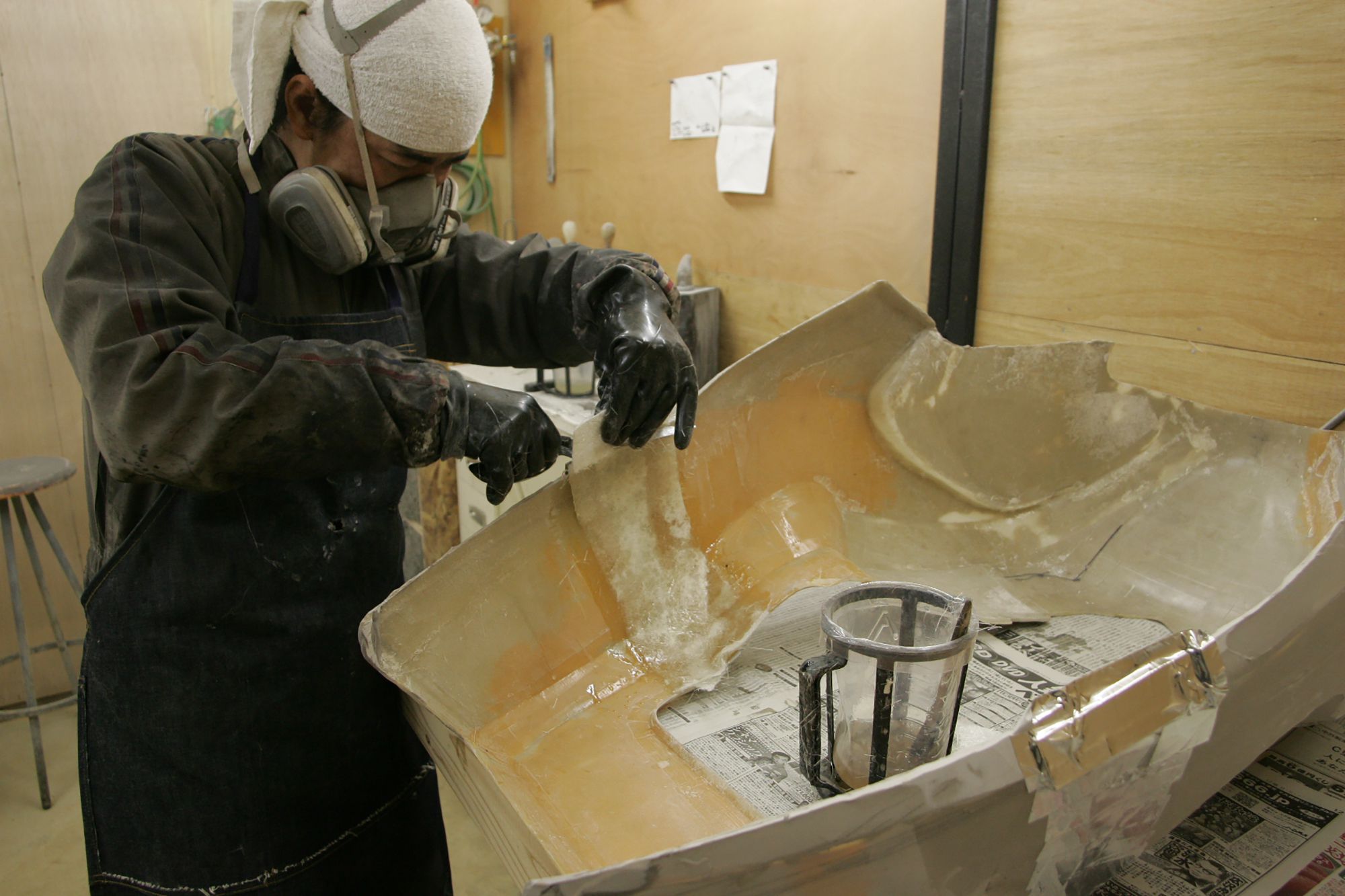
適度なサイズにカットしたファイバーに樹脂をつけてあてがってみる。更に不必要な部分があればカットします。
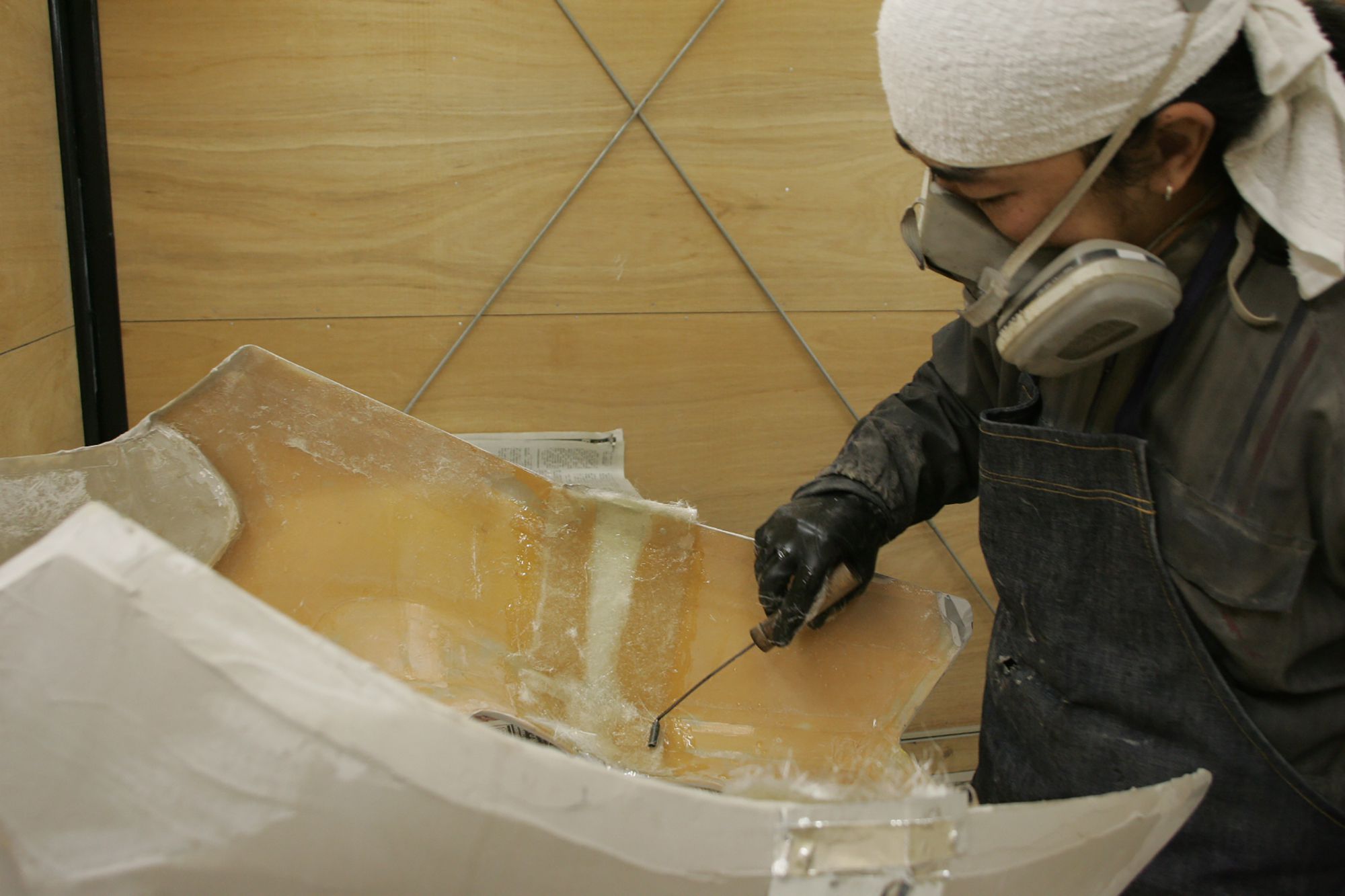
脱泡ローターで丁寧に気泡を抜いていきつつ、必要な厚みになるようにしていきます。
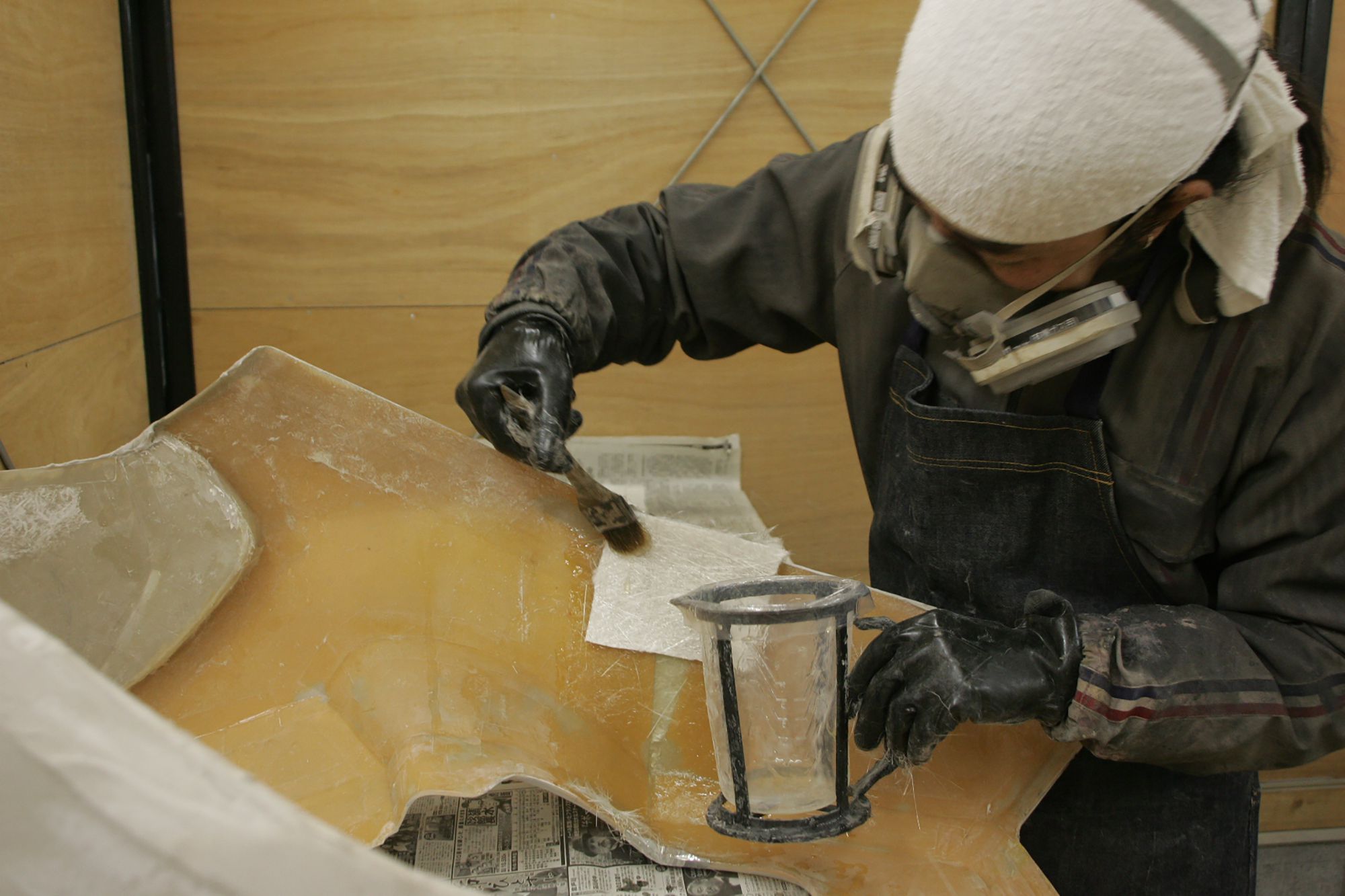
ファイバーは1枚貼って終わりではなく、2枚にするなどで強度を保つこともお忘れなく。
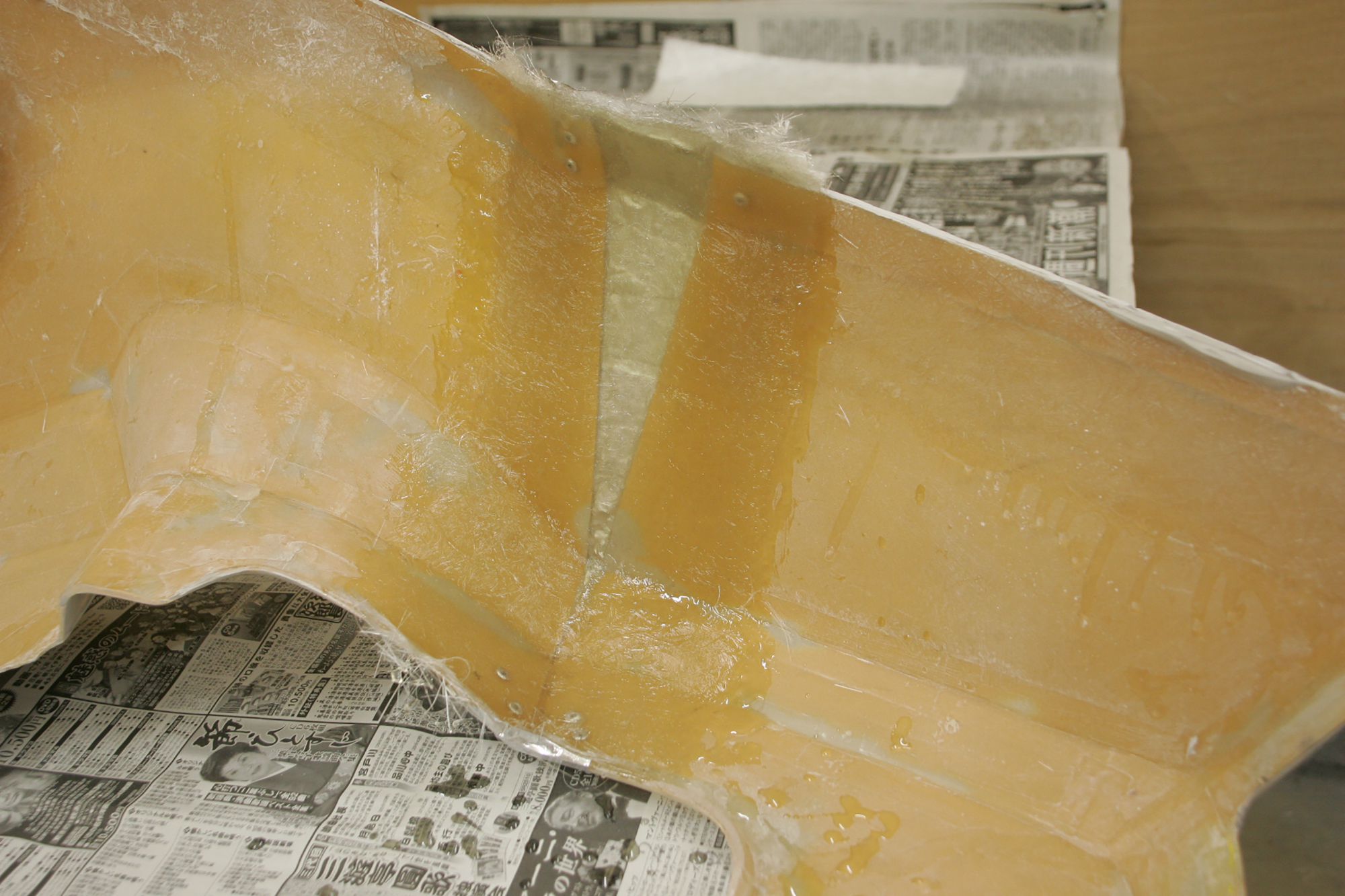
これがファイバーを貼り終えた状態。あとはこれで硬化するまで待ちます!
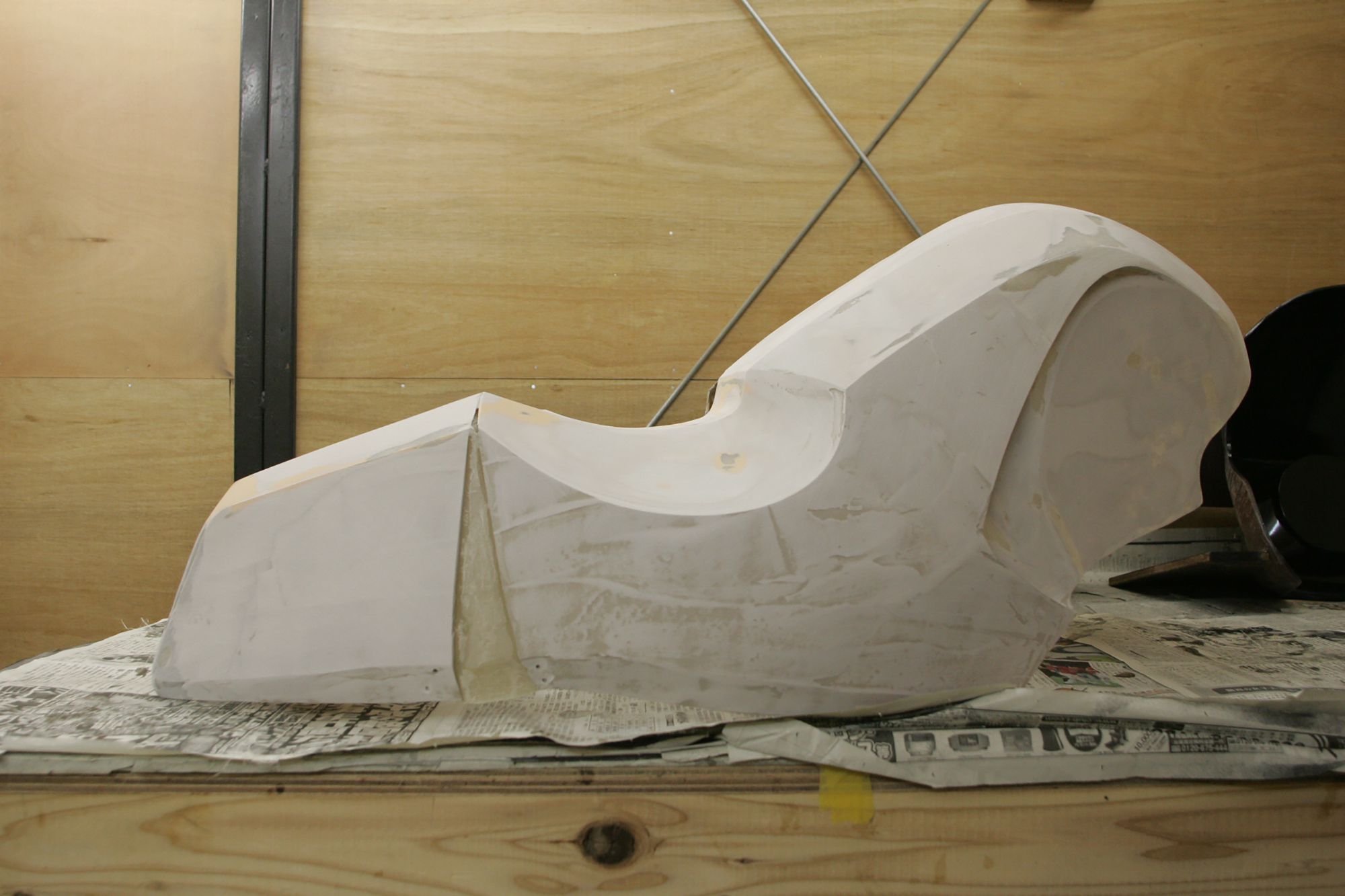
FRPが硬化したらアルミのステーとアルミテープを剥がして、表面にパテを盛って成型していきます。
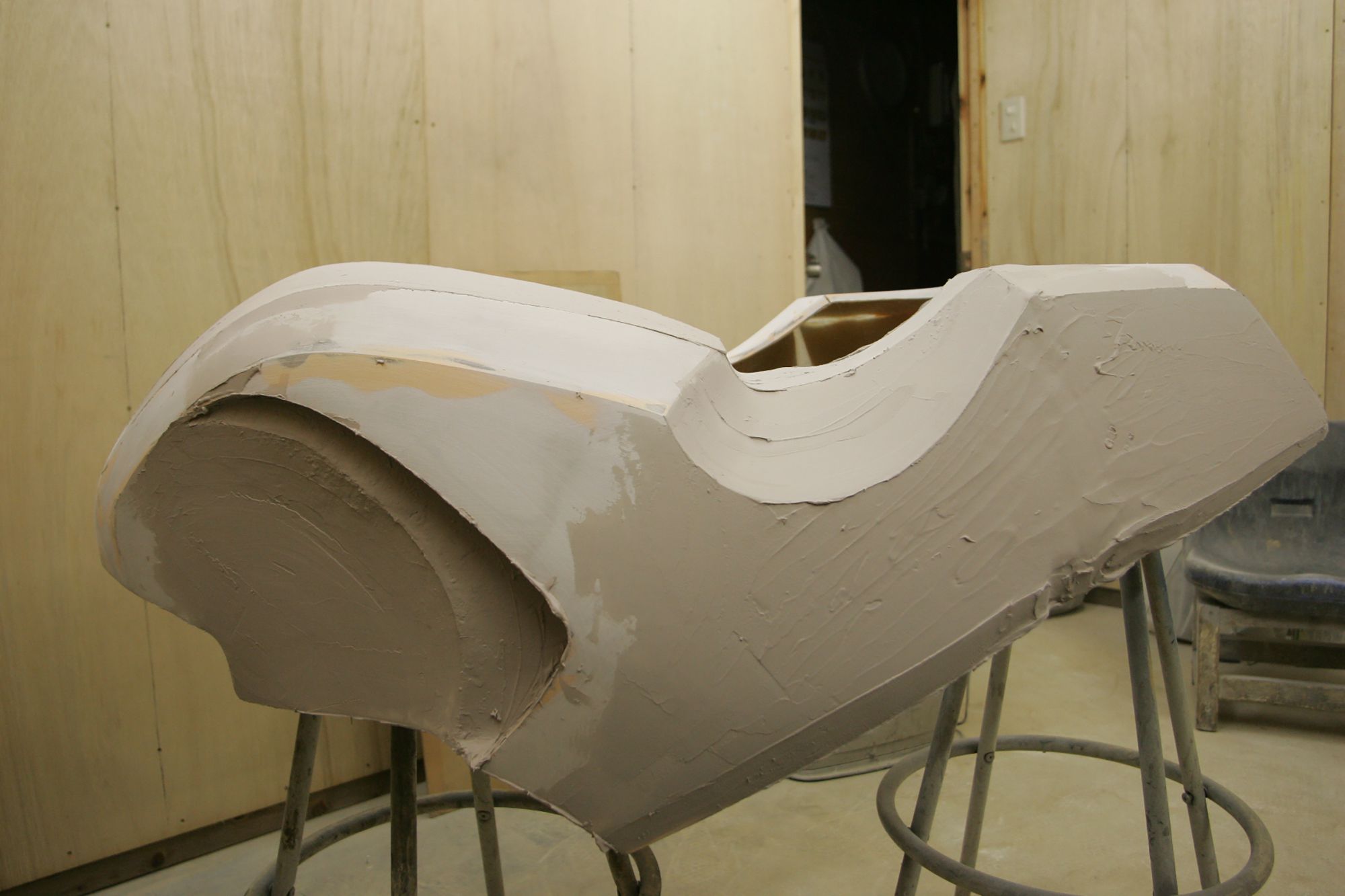
パテはピンポイントに盛るのではなく、その周りも含めて全体的に付けていきます。
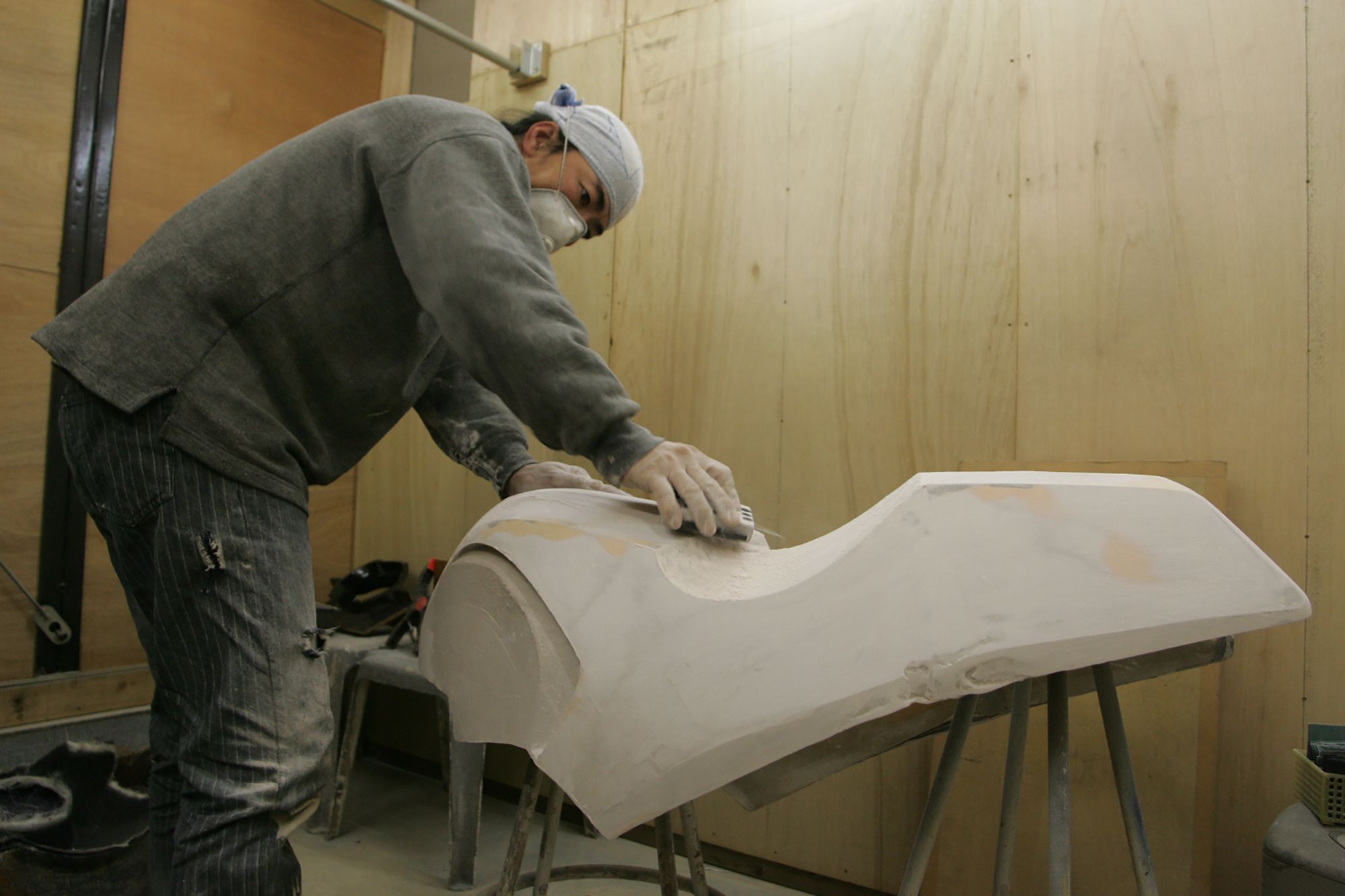
パテを硬化させたらあとはひたすらサンドペーパーを当てて削ります。
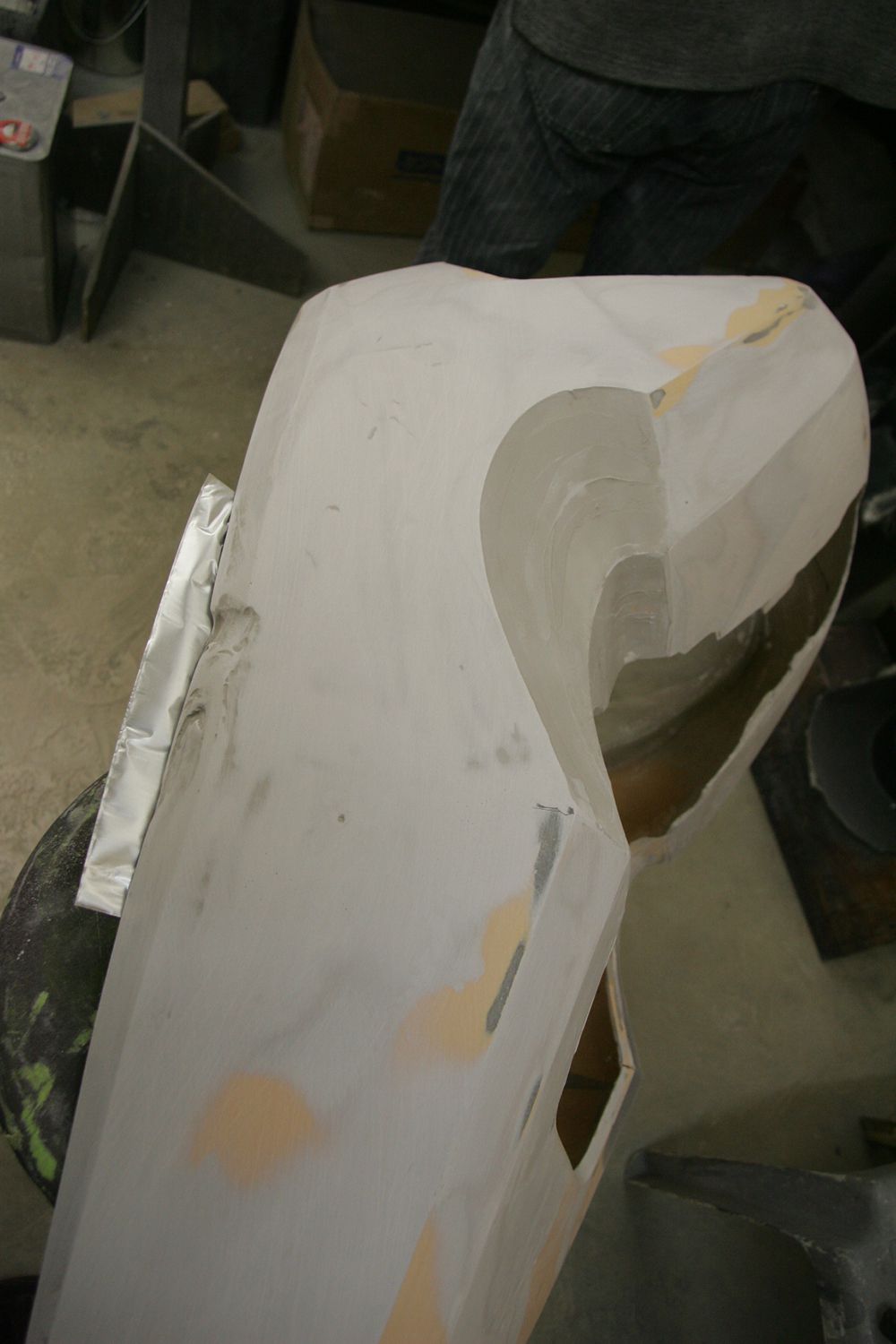
カウル下側の折り返し(アルミのステーをリベットで止めていた下側の部分)は逆アールになっていて、どうにもパテが垂れやすい。そこでアルミテープを貼ってパテの受けとして使います。
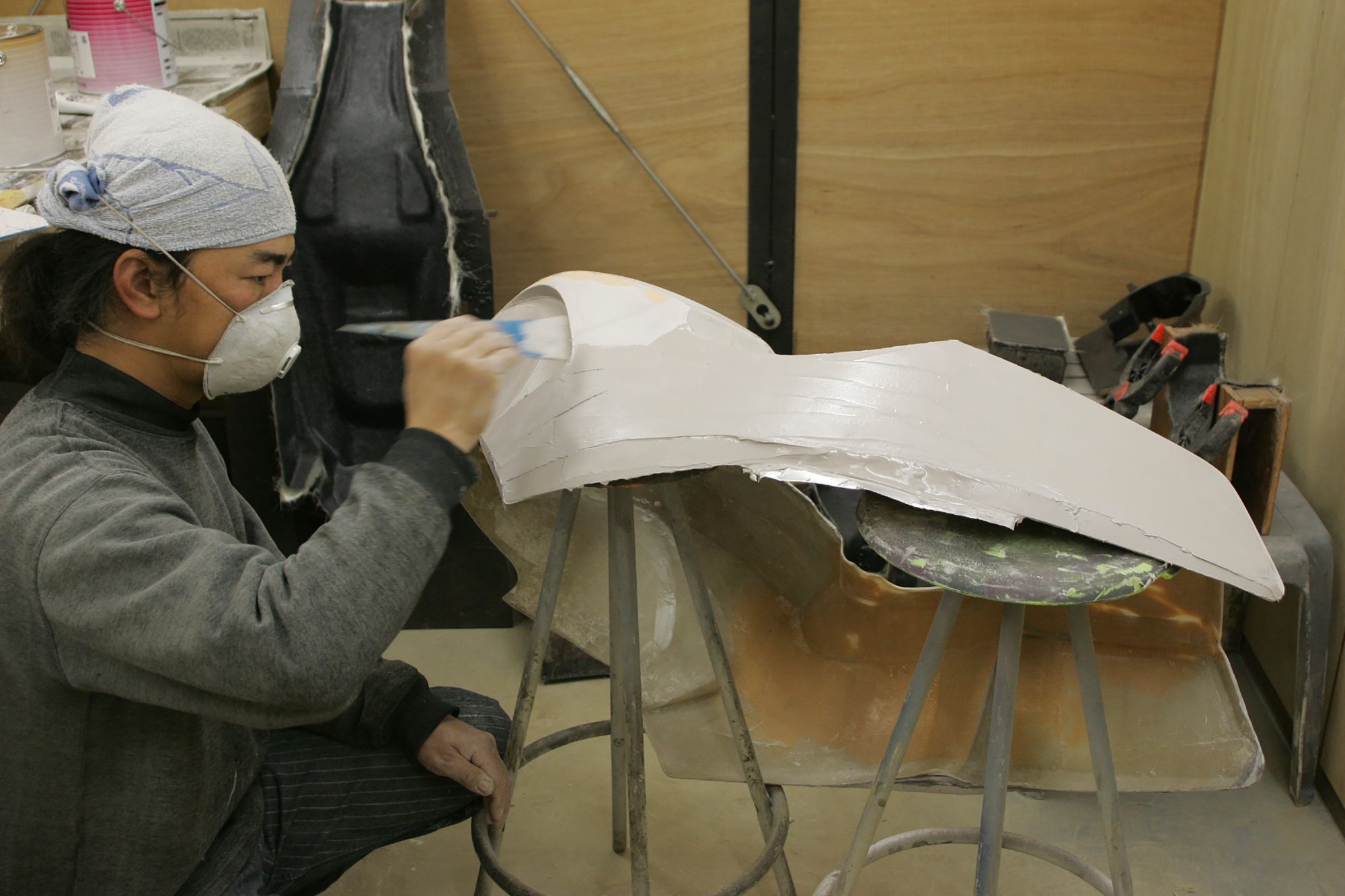
何度もパテを付けては削っての繰り返しの作業だ。しかしアッパーカウルは行程を踏むたびに、少しずつ成型されていくのだ。
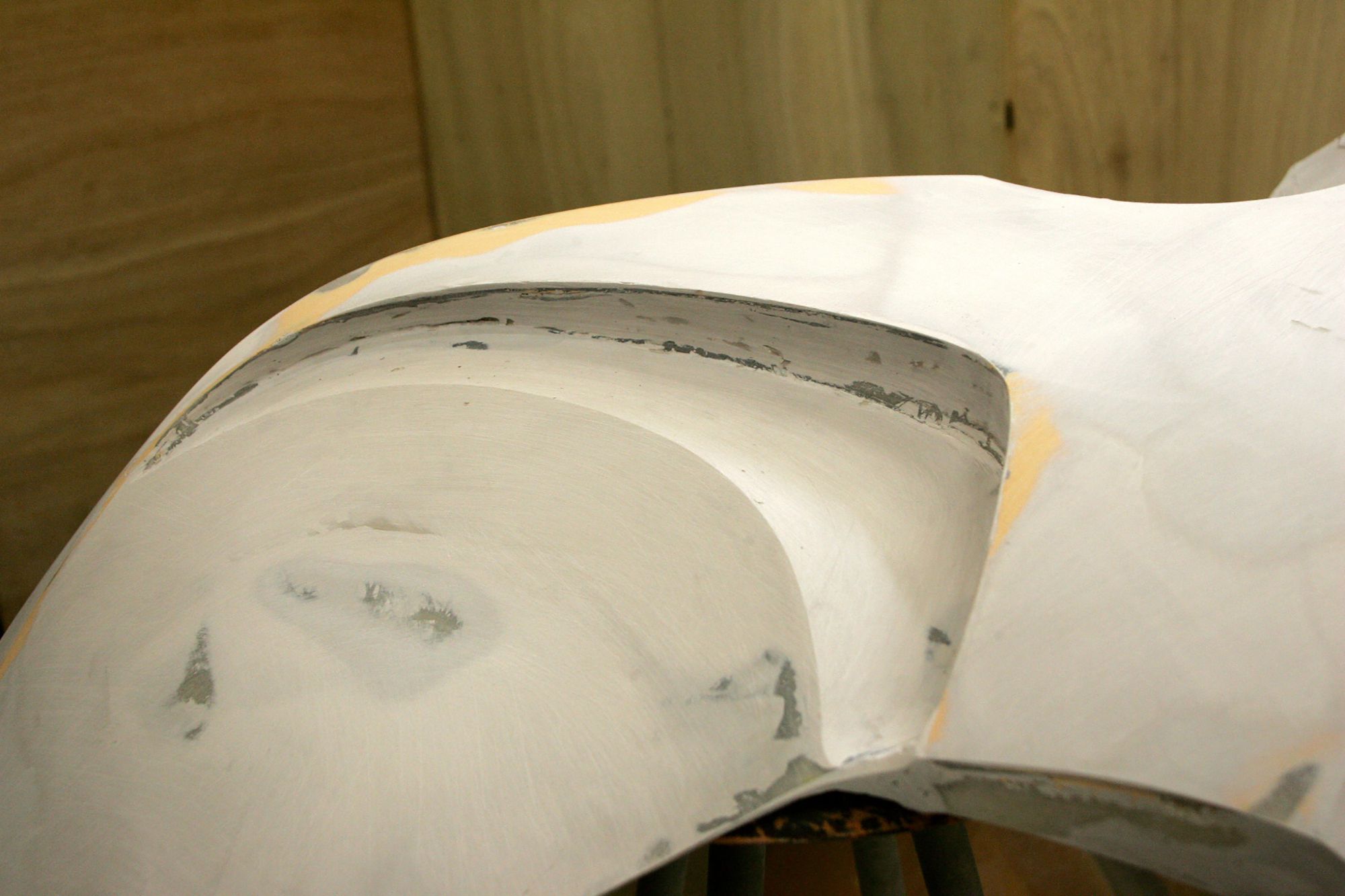
タンクサイドには内側にダクトを造形していきます。でもこういった入り組んだ部分はまた、手が入りにくいので大変なのだ。
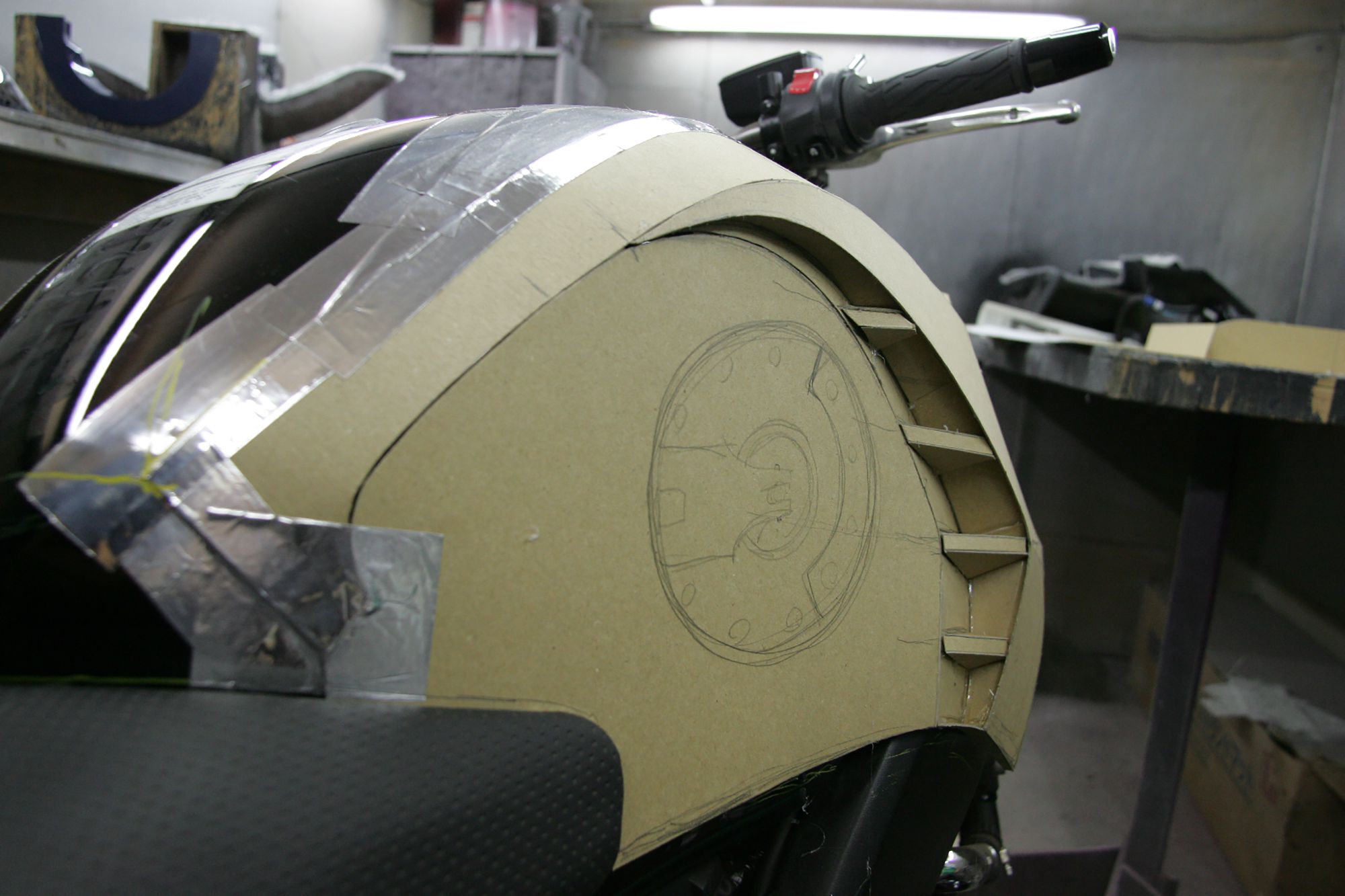
Vol.09の時はダンボールで仮に造ってみたけど、今度はこれをFRP原型に造形していくのだ!
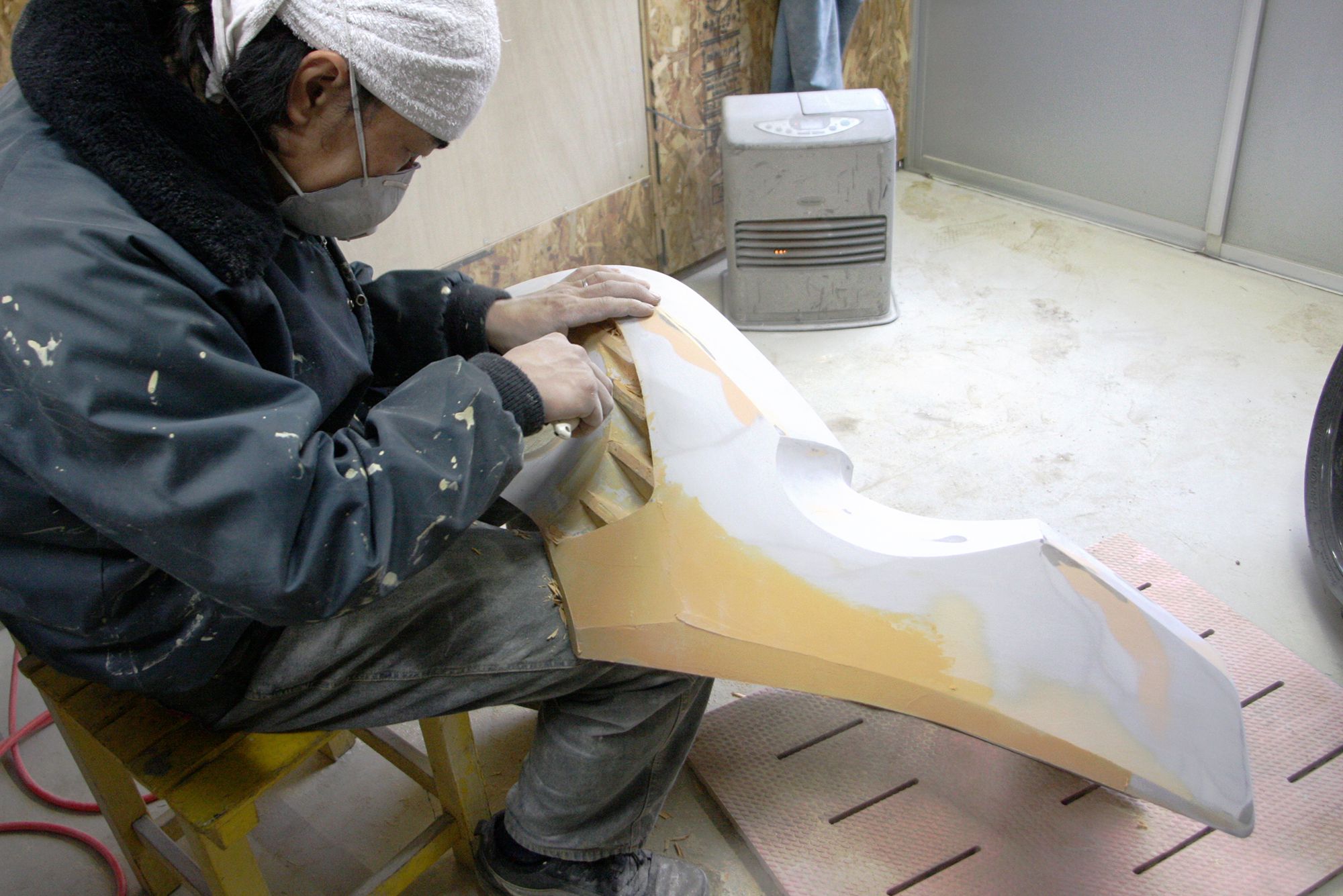
というわけで、続いてはサイドダクトの造形に取り掛かることになりました! ダクトはこのバカデカイアッパーカウル内に溜まるであろうエンジン熱を逃がさなきゃならないこともあるし、デザイン面だけではなく構造的にももはや必須項目!

人気コンテンツ
-
BBB Staff BLOG
2021.03.17
販売証明書の書き方を掲載!原付二種ナンバープレートは市役所で取得できます
新型コロナウイルスの感染拡大に伴い、三密を避けることができる手段として注目を浴びているバイク。そ...
-
BBB Staff BLOG
2019.05.31 / Vol.22
【2019年版】ミニカー登録まとめ
BBBマガジンの記事ではミニカー登録についてキーワード検索されているのが多く、需要がありそうだったのでミニカー登録につい...
-
BBB Staff BLOG
2020.11.11
実は簡単⁉市役所に行くだけで完結 原付一種ナンバープレート取得までの手順をご紹介
近年、EVモビリティやキックボードなどが登場し、若者を中心に多くの人から注目を集めている原付一種(50㏄)。けれども、意...
-
大人のたしなみとしてベスパに接してみよう!
2015.06.03 / Vol.12
スモールで遊ぶ #01
さてさて今回からいよいよ「スモールで遊ぶ編」をお届けしますよ〜......って、スモールってなに? となっちゃいますよ...
-
レストア野郎★Zippy編
2014.01.11 / Vol.05
ホイールとエンジンを自家塗装してみよう! ペイント編
スポークホイールのペイントとなると、一度スポークをバラしてハブもリムも磨くのはもちろん、スポークも1本ずつ磨いてからの作...
-
プロトモスピーダ
2008.08.07 / VOl.09
アッパーカウル製作1
ボール紙を切って原型の元となる形状を作り上げていきます。出来上がったら上にFRPを貼っていくので、ボール紙といってもある...
-
レストア野郎★2番星★FTR250編
2014.10.28 / Vol.04
タペット調整でエンストするエンジンが快適になるとイイナ!
Vol.04 タペット調整しましょう! タペット調整とはカムシャフトとロッカーアームとの隙間であるバ...
-
BBB Staff BLOG
2018.09.20 / Vol.17
今こそ2ストに乗ろう!2018 〜2ストの魅力をどっぷり解説〜
オートバイは走るシチュエーションや、ネイキッド・クルーザー(アメリカン)・オフロード(モトクロス...
-
BBB Staff BLOG
2019.10.29
ツーリング動画を撮影したい!必要なものや撮影の手順を紹介!
ツーリングでは、自分の好きなルートを選び、バイクを走らせながら周囲に見えてくるさまざまな景色を楽しむことができます。そん...
BBBマガジン
この記事の日付(2009.02.17)に近いコンテンツ
-
全国「旅ごはん!」バイク紀行
Curry Coffee弱尊(ジャクソン)の飛騨牛スジカレー(岐阜県高山市)
2010.03.25 更新 / Vol.03
-
全国「旅ごはん!」バイク紀行
Cafe SofariiのつけナポリタンSofarii風(静岡県富士市)
2010.02.25 更新 / Vol.02
-
全国「旅ごはん!」バイク紀行
住吉飯店のもやし麺(千葉県南房総)
2010.01.25 更新 / Vol.01
-
BBB Staff BLOG
スーパースポーツとMotoGPマシンを紹介
2008.12.27 更新 / Vol.06
-
藤原かんいち電動バイク世界一周 夢大陸オーストラリア編
「砂漠に倒れる!」
2008.11.24 更新 / Vol.45
-
藤原かんいち電動バイク世界一周 夢大陸オーストラリア編
「バイクを返せ!」
2008.11.24 更新 / Vol.44